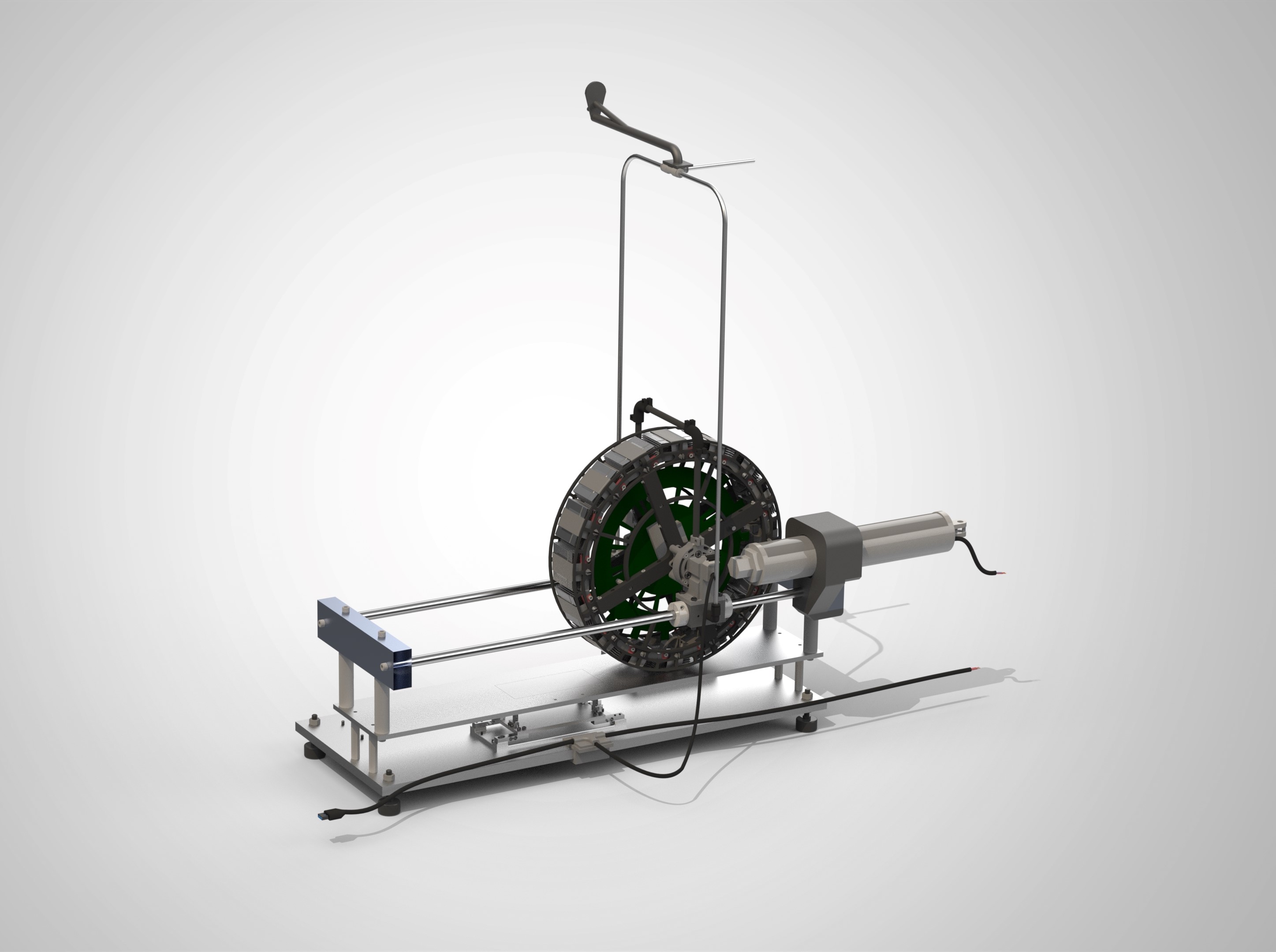
Authors: Khoi Ly, Kyle Martinaitis, Mark Rentschler, Nikolaus Correll
Submission: In preparation
Description
Although we presented a mathematical model of the soft rolling robot driven by electro-hydraulic actuators and the validity of the model in the context of control, there were a few significant assumptions made to make the controller possible. Among those assumptions, the actuation force function for the robot’s acceleration and deceleration plays a crucial role in not only the accuracy of the mathematical model of the rolling robot, but also affects how the controller is designed. Specifically, a more accurate actuation force model for acceleration and deceleration allows for better estimate of the power output of the robot, eliminate the need of disturbance error accumulator, and improve the estimate of angular speed for control.
To achieve a more accurate actuation force model, we aim to evaluate the actuation force’s amplitude, direction, and equivalent point of contact in both acceleration and deceleration. Due to the soft nature of the mounted folded-HASEL actuators, the actuation force between the actuator and the ground might not goes to the center of mass of the robot, as assumed previously. The misalignment of force direction not only changes the magnitude of the horizontal component, but also generate a moment around the center of mass of the robot. The evaluation of the force functions and its direction relative to the robot’s COM inspire the study in this chapter.
The aparatus for force characterization consists of 8 load cells, four (rated at 780g load) of which are to sense the normal forces and the remaining four (rated at 150 g load) are to sense the tangential (shear) forces. To help examine the speed-dependent nature of the actuation forces, the aparatus also contains a speed-controlled linear motor to generate consistent initial robot’s translation speeds and a photointerrupter sensor to measure the instantaneous speed at which the robot slides over the force sensor. The force data (sampling rate: 4 kHz) generated by the load cells and collected by a NI-myDAQ device, the IMU data (sampling rate: 400 Hz) collected by the onboard microcontroller, and the instantaneous speed data (sampling rate: 400 Hz) collected by the second Teensy microcontroller are hardware-synchronized and received by a parallel program (spmd) on Matlab.